Compact card - The future of carding
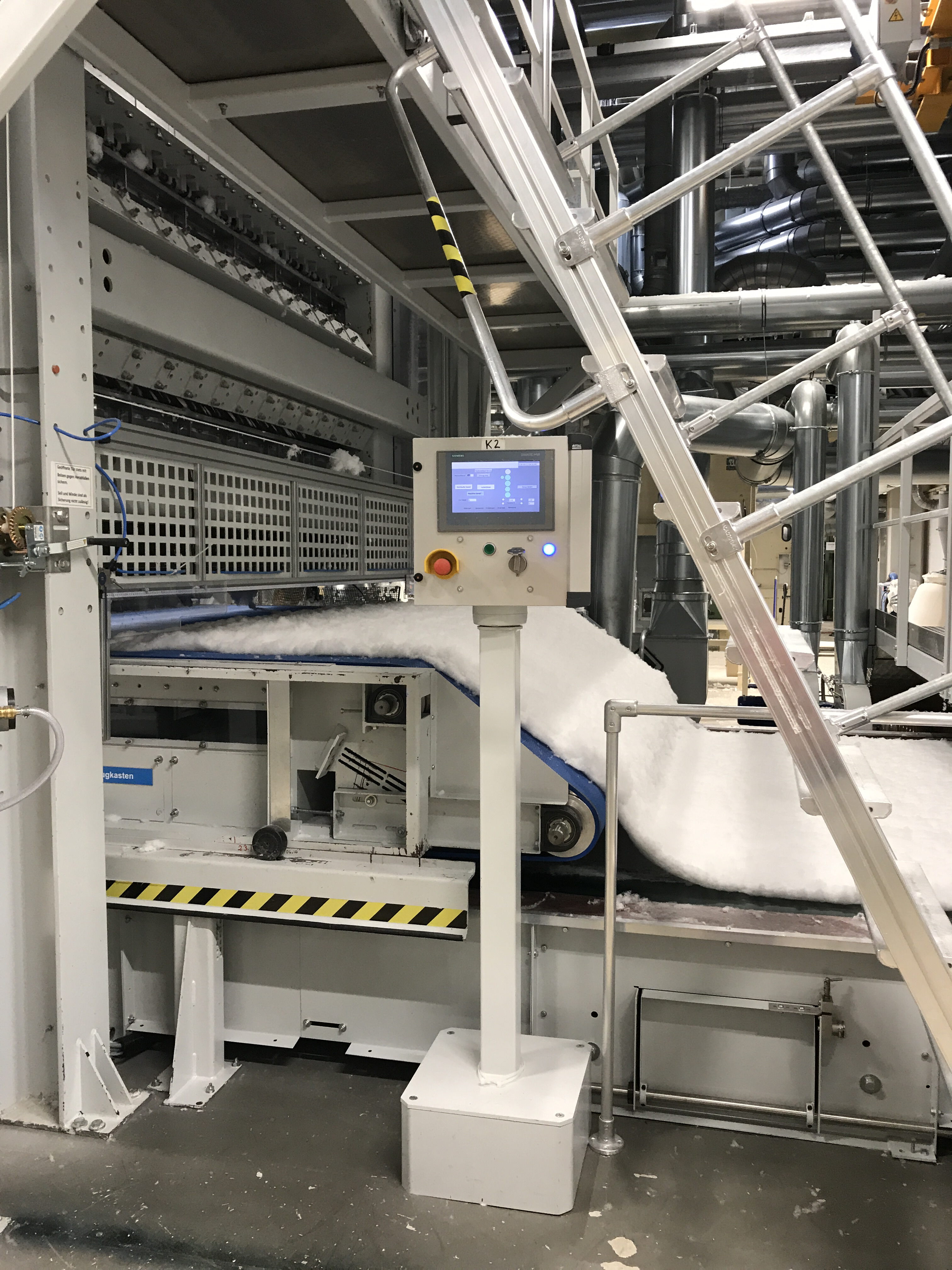
Universal carding unit for roller/ aerodynamic doffing
10 years compact card! Read more
In short: the benefits of the Compact Card. Read more.
The HERGETH name is known for its long tradition of innovative solutions for the nonwovens industry. In keeping with that tradition, the HERGETH carding unit offers many new and unique advantages in efficiency, operation, web forming and maintenance.
The process starts with our new fine opening unit that allows the feeding to the card with very low air volume and produces very finely opened fibres.
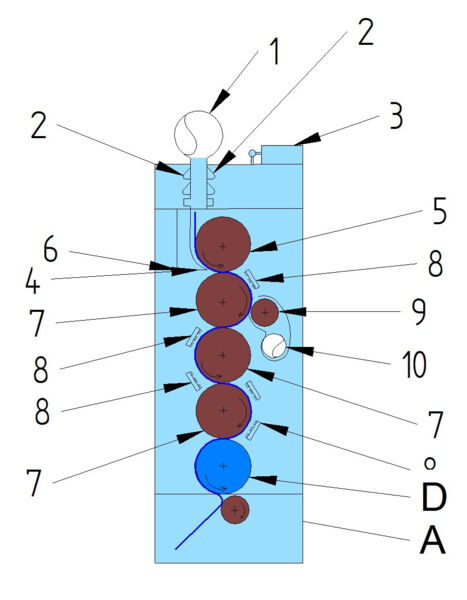
The new High Precision Chute (1) ensures a good material feeding to the card. In the chute, the fibres are separated from the air by progressively profiled blade bars (2). This profile reduces the risk of fibres intertwining around the bars and blocking the system. The chute is made of segments that set the chute feed depth by electronic linear units (3). The fibres leave the chute feed and are pressed to the feed roll by segmented pneumatically loaded feed plates (4). The pressure can easily be set on a central valve to adjust to different blends. This ensures good control of the fibres also on very wide cards. The pivoting of the segments is measured to determine the fibre distribution. A PID regulator controls the linear units that position the segments of the chute to achieve a uniform weight across the width of the web.
The fibres enter the card through a large diameter feed roll with unidirectional feed (5). The feed table (6) is very large and strong. A large diameter of the feed roll ensures better control of the fibres entering the unit. The three main cylinders (7) have the same diameter. The use of three cylinders ensures that the fibres are accelerated gently and carded from both sides. The carding is done by up to fifteen carding strips (8), producing a carding power that is similar to a conventional card equipped with multiple rollers and strippers. The carding strips are easily exchanged and are moderately priced. The carding strips can be adapted to the material processed. The strips can be replaced with blanks when less carding power is required.
A unique new feature is the H2 roller (9). This roller skims the surplus fibres from the first cylinder. The surplus fibres are sucked off (10), and reintroduced to the feeding machine thus reducing the chances of thick spots and clouds.
The carding feed and carding unit are always the same for all applications. The system is processing fibres from 10 - 100 mm length and fibres from 0,9 dtex up to 100 dtex and coarse wool, and bleached cotton.
In order to optimize products different outlet configurations can be fit to the machine at any time:
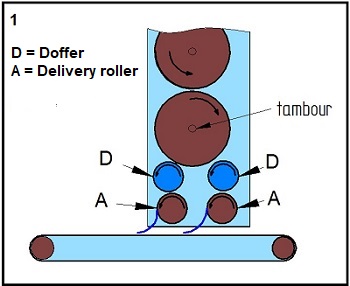
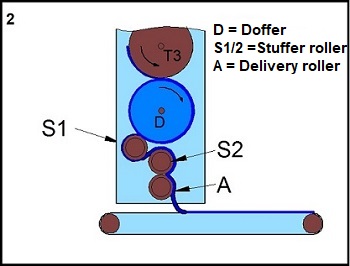
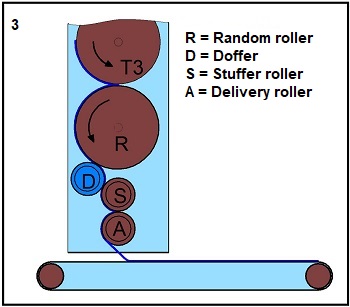
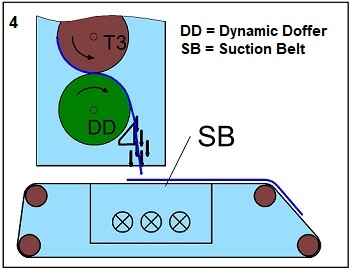
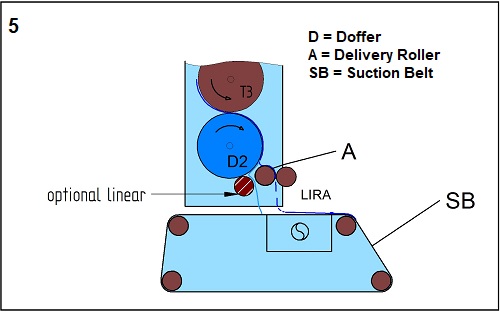
The LiRa (linear/ random) card combines the regularity of roller-doffed carding with the random effect of aerodynamical carding to produce light weight regular isotropic webs. Linear webs or heavy weight aerodynamic webs are also possible within only a few minutes required to change over.
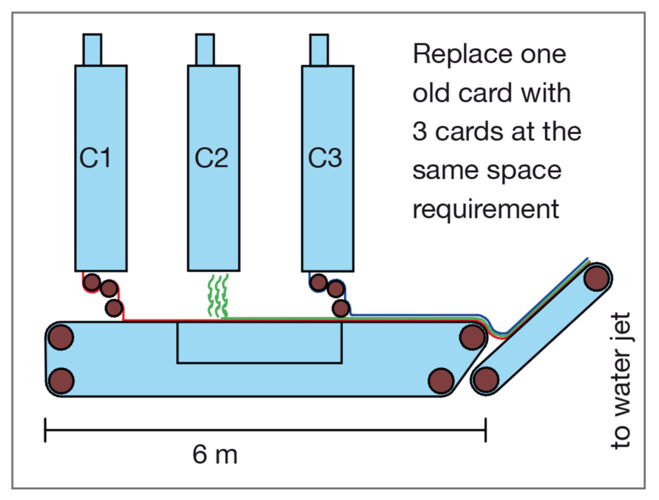
The design of the compact card had the future markets for cards in mind.
- extreme flexibility to produce a big variety of webs with different fibres
- possible to produce multi-layer products
- short staple cotton and flushable fibres
Minimum space is required for a compact line for 3 fibres with 2 roller-doffed and one airlaid layer: The standard in hygienic products today.
This method allows for the creation of a single web out of two layers that are oriented at an angle of 90° with respect to each other.
This unique process allows for the creation of new nonwoven products.
A machine with one cylinder and no carding elements, but with a stripping roller, is used for coarse products. This machine, with double-sided suction, can also form very heavy webs.
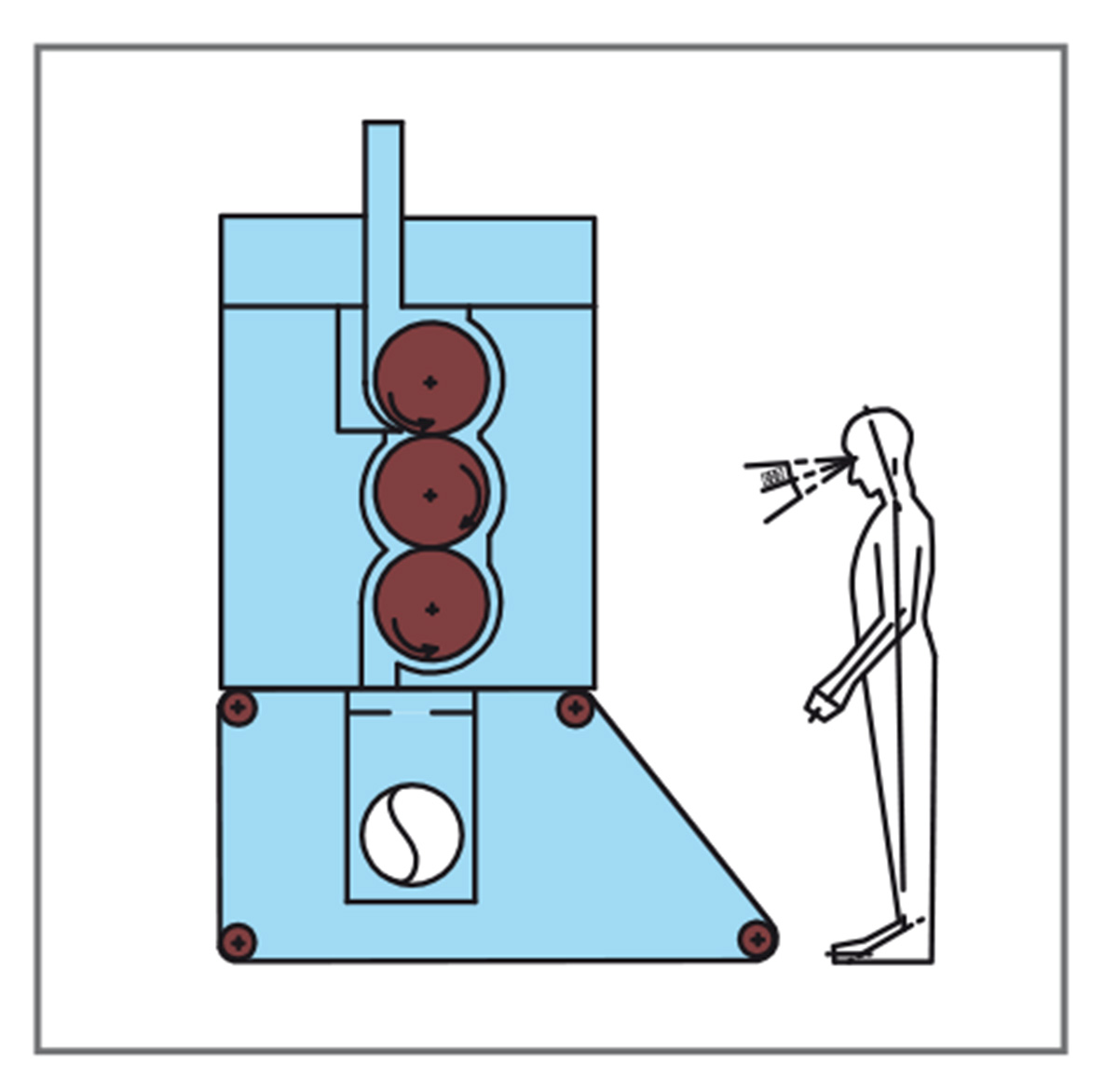
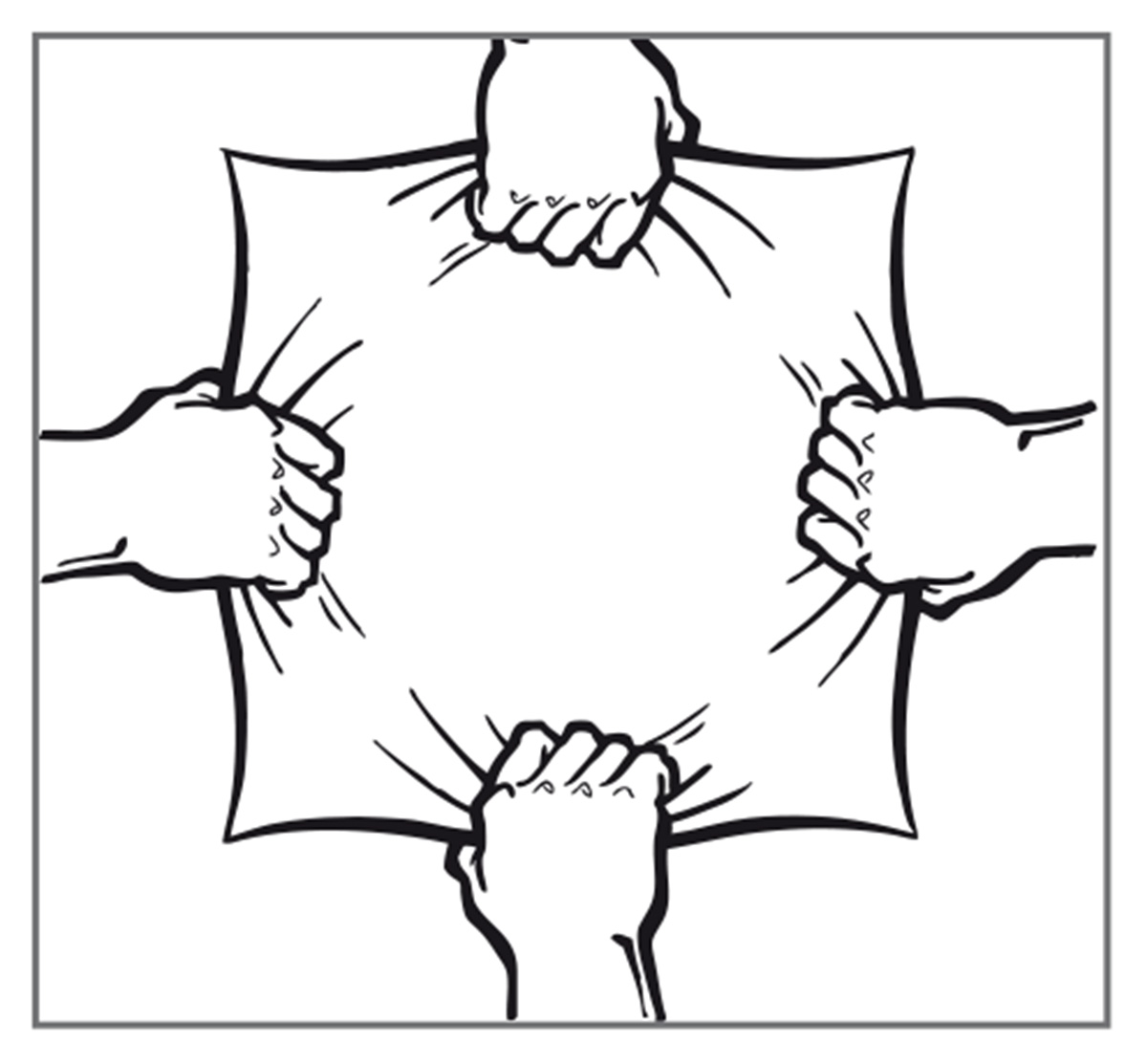
Simple operation and low maintenance were the main reasons for creating the new card. Spare part costs are low since only two roll diameters are used. The rolls may be easily taken out, with the bearings on their shafts, to allow for rapid product changeover or for quick servicing. All roll drives are concentrated in a drive tower separate from the carding unit. The rolls are directly driven with cardan shafts thus avoiding belts, chains, and hidden motors in the machine. The shafts are not affected by rotational loads avoiding broken shafts.
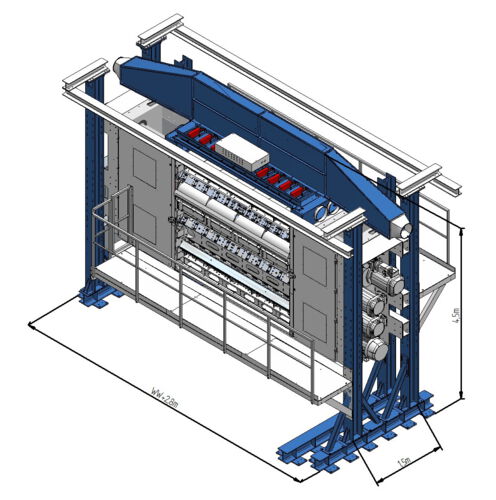
All motors are easily accessible. Feed, doffer, delivery rollers, and the stuffer rollers, if used, are all servo-driven. The three carding rolls and the stripping roller, if used, are frequency-controlled for quick speed changes.
All drives are SEW and the PLC is a Siemens S7 type.
The vertical arrangement of the card allows for easy access of rollers and carding elements. The setting of the rollers is done in only one direction and the setting of the carding elements can be controlled along the width of the carding cylinders. Air flow in the machine is top-down which reduces fibre accumulation. All carding cylinders and the feed roll are fully shrouded. Ample windows allow to view the cylinders even in applications with limited space. No sub-frame is necessary as the machine is bolted to pillars. The card may easily be integrated into an existing production line.
Background information 1: Setting of the compact card (German)
Background information 2: Why a new card?
Background information 3: Warum funktionieren Kardierstreifen? (German)