OPTiMETER-S
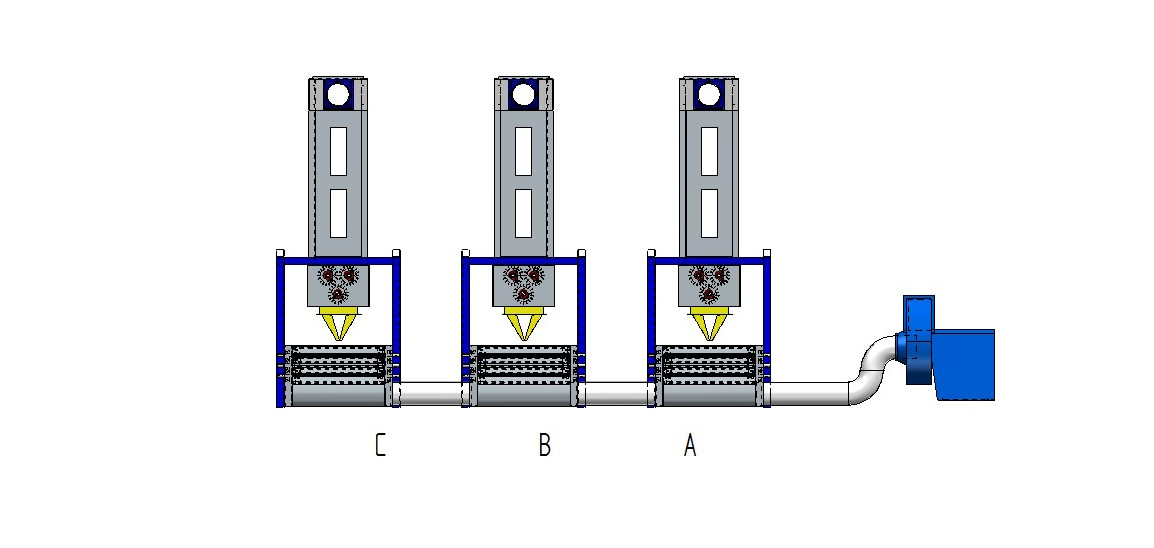
With the density-controlled blend line OPTiMETER-D it was possible to blend huge amounts of fibers at very small space. It also allowed us for the first time to serve several lines with different blend ratios with just one blend line.
Some of our customers need a gravity weighing process to document their blend. In order to bring the benefits also to the weighing process, a new way to do the job was necessary. The old way of weigh blending since decades is to place several bale openers with weigh scales in a line and each component is dropped on the previous as the belt processes. So fibers dropped at the same time do not form the blend at the same time.The new way is to have the fibers that are dropped at the same time form a blend at the same time. Each of the weighing towers that have huge weigh scales up to 3 meters wide drop the fibers on their own small belt at the same time. Then all belts proceed to their own individual opening unit simultaneously. So the fibers that have been dropped at the same time are opened at the same time and the resulting fine tufts are mixed in a common suction tube. This allows to change the blend ratio after each drop and send the fibers of the simultaneous drop to different lines. By this, different lines with different blend ratios can be fed by just one blend line. A huge saving.
The old way to manage small components of about 1 % was to add a small scale to the blend line. This is not necessary in our weighing system. The scale is filled and drops an amount of fibers that is equivalent to a 10 % load, but the individual collecting belt just runs with 10 % of the speed of other bels resulting in adding only 1 % to the blend.
By this, additional small scales are not necessary and high capacities of 2000 kg/ h and more can be achieved by each component (most applied at multi line process).
The individual opening allows better space utilisation and easy add-on of more components.
Background information: Blending